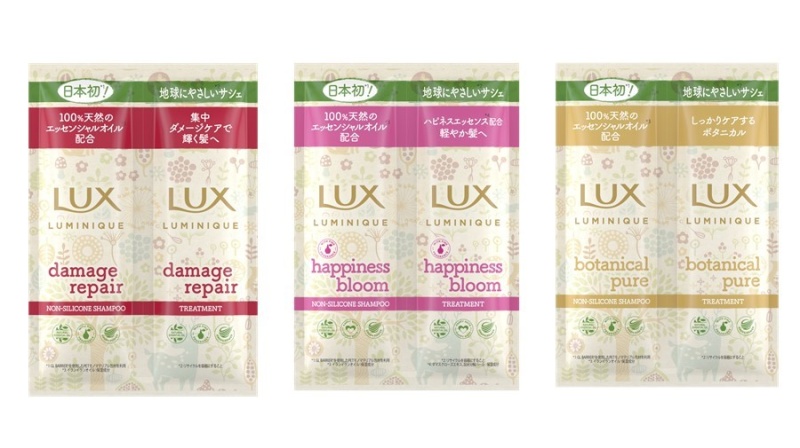
29 ก.ค. Check out Top 9 advancements in monomaterial plastic – 2021
Why have we designed multi-layered flexible?
The dominant plastic packaging, which includes flexible films, lid, cups, and pouches for FMCG, baby food, frozen, pharma, PET food sectors needs on the shelf, is a composite material.
It is designed for OTR & WVTR barrier, preventing oil and microbial protection from penetrating the packaging. And whist this packaging has traditionally created the most desirable outcome, but the packaging is difficult to recycle. The recycling number is 7.
A sweet story of recycle logo and plastic
There is an apparent reason for the addition of composite plastic with many benefits in a single shot. In case if we have a multi-layered flexible pouch that can have top to innermost layer is PET/AL/LDPE (assumption). We all know that the inner layer of the pouch is LDPE is for the sealing purpose, and then aluminum has the advancement of the best MVTR and OTR barrier. And the top layer of PET is the reverse printing benefits.
Concern
Recycling cannot be accessible with composite materials; these plastics cannot be traditional mechanically recycled. And need to be separated; if not, the quality of the recycled plastic (which has a higher recycled value) will be lowered or even contaminated beyond reusability.
The reverse engineering of plastic (such as recycling) into specific materials follows the same process. Recycling could be an energy-intensive activity, but it closes the loop for a circular economy in packaging products. However, the more complicated a packaging design, the more effort is needed to recycle it.
Unfortunately, the only way to know if this mixture of inseparable materials is durable or toxic is to test it. Still, the composite plastic is rendered non-recyclable after that.
The increasing concerns around sustainability, from businesses and consumers, have shifted the spotlight to mono-material flexible packaging.
Shifting to Monomaterial Packaging
With the research and development into mono-material flexible packaging having advanced the available products to meet the high barrier and shelf-life requirements for food packaging, this option is a viable alternative to the difficult to recycle composite-material product that is still dominating the shelves.
There are numerous players involved in the lifecycle of one product. It may not be sufficient when only one of the players upstream creates a ‘circular product’ without affecting the other downstream to ensure that the loop can genuinely be closed.
Packaging made of mono-material consists of several layers of a single primary material. This allows for more sustainable production and easier recycling. There are many possible applications – but only if all the advantages of conventional packaging are retained. After all, mono-material packaging must also be flexible, lightweight, easy to print, and easy to process on customer equipment.
What is Monomaterial packaging?
- Monomaterial packaging includes only one type of plastic.
- Monomaterial packaging only consists of a single material they are easily classified for recycling, compared to packaging made with multiple materials.
- Typically packaging contains various materials that would need to be taken apart by each material, but with mono-material packaging, consumers don’t need to disassemble the product before recycling. They can pop the entire empty product into the recycling bin.
- Therefore Mono-material packaging can easily be recycled, reused, and repurposed, giving the product a longer life cycle.
So, let’s check how our industry has adopted the change of monolayered plastic for their product.
1. FMCG Packaging
a. PET based monomaterial film – Toppan
Conventional individual packages combine a PET substrate with materials such as aluminum and polyethylene. Toppan’s mono-material packaging uses a PET-based grade of GL FILM, a market-leading vapor-deposited transparent barrier film from the GL BARRIER range, and combines it with PET sealant.

The manufacturing method and material composition ensure outstanding oxygen and water vapor barrier performance, provide low adsorption to prevent loss of aroma and quality, and make it possible to avoid the reduction of product weight during storage over long periods. Using a single material improves recyclability, and the absence of aluminum film enables a decrease of roughly 25% in CO2 emissions during packaging manufacture.
Alternative to PET/AL/LDPE
BY TOPPAN
For specific products, we, therefore, suggest the use of flexible mono-material laminates. Instead of working with laminates composed of different materials such as PET/ALU/PE, selecting only one laminate material is possible and meaningful.
It can produce laminates that are easier to recycle based on mono-material PP, with or without barriers. Because of the new packaging legislation, this choice is undoubtedly a great alternative to conventional laminate materials.
b. Olives snack pack – Hatzopoulos S.A.
Greek olives producer GAEA has partnered with A.Hatzopoulos S.A. to launch its first recyclable, mono-material olives snack pack.
The previously conventional packaging film used for this product was completely redesigned to meet the latest guidelines for recycling while it maintains at the same time its high-barrier properties. The mono-material, all-PP packs have been certified by Interseroh and carry the “Made for Recycling” mark.

The solution was brought by Hatzopoulos S.A. based on X-CYCLETM packaging technology.
The packaging structure was completely redesigned. The new recyclable PP-mono-material film that was finally developed enabled a smooth switch from a conventional film formulation to a recyclable one with a better environmental profile, achieving -20% plastic packaging weight reduction and resource-efficiency sustainability benefits.
2. Food Packaging
a. Coffee Packaging
The Gualapack suggests a complete range of laminates for coffee packaging, highlighting high mechanical performance and total protection from gas and moisture to preserve fragrance and aroma.
The coffee industry now allows mono-material PP laminates. Made of high-performance and tailor-made polypropylene resins, they are designed to collect, sort, and recycle in the PP stream.

b. Processed marine products, pickles and prepared foods packaging – Mitsui Chemical
Frozen food, processed marine products, pickles and prepared foods, liquid food (soups and seasonings), refill containers (standing pouches), heavyweight products such as rice, etc.

TUX™ is a Metallocene LLDPE film manufactured by the T-Die cast method using 100% HAO (C6) resin.
T.U.X™ is 100% Metallocene L-LDPE component T-Die cast film
- Excellent heat seal strength
- Excellent thickness uniformity
- High transparency
- Seal through contamination property
3. PET Food Packaging
a. PE-based film – ProAmpac
ProAmpac announces the launch of R-2000D, their newest patent-pending addition to the ProActive Recyclable® series of polyethylene-based structures. Designed to be a drop-in replacement for conventional multi-material laminates, R-2000D’s unique performance characteristics allow it to run on form/fill/seal equipment at high speeds.
R-2000D is the newest member of the ProActive Sustainability family and is available in standard, high barrier, and ultra-high barriers to extend the shelf-life of dry products. Both standard and high barrier platforms have been tested and pre-qualified for polyethylene store-drop-off recycling.

R-2000D offers high clarity, high drop resistance, excellent stiffness, and dimpling resistance for premium shelf appearance. R-2000D provides perfect directional tear without laser scoring, and R-2100D provides improved toughness for sharp products like nuts, pet treats, and pretzels. With superior heat resistance, R-2000D allows for optimal speeds, a wide operating window, and high filling efficiency.
b. Recyclable dog food packaging – Mondi and Vafo Group
The new packaging satisfies the pet food producer’s objective of launching a reclosable and recyclable packaging solution that does not compromise the achievement and retains strong brand identification in stores. It also speaks sustainability concerns of end consumers who play more extra in purchasing pet food and products.

The beforehand unrecyclable multi-layer packaging contained a metalized layer substituted by Mondi’s recyclable mono material packaging: a reel material for form-fill-and-seal (FFS) 1.5kg bags pre-made FlexiBag Recyclable for bags up to 15kg. FlexiBag Recyclable is a mono-material polyethylene (PE) pre-made bag explicitly produced for recycling, which means it can be deposited straight into Finnish plastic recycling streams.
4. Aerosol Packaging
a. Monomaterial pump – Aptar
It launched the first fully recyclable mono-material pump for the beauty and personal care industries, called Future. Certified and Sustainable by Design To facilitate recycling, Future was designed using polyethylene (PE) mono-material. Future is certified by Cyclos-HTP, the institute for Recyclability and Product Responsibility*. The innovation is also recognized “A” by RecyClass – a comprehensive cross-industry initiative that works to establish a harmonized recycling approach.

b. MonoMaterial sustainable and recyclable dispenser pump – TriMas
The highly innovative MonoTM-2e was identified as a 2020 finalist of the Sustainability Packaging Coalition Innovator Honors for the revolutionary single-polymer design. The registered pump features six parts, all made from one polymer. It is 100% recyclable and designed to decrease its carbon footprint significantly. In expanding, the MonoTM-2e is e-commerce available, minimizing the risk of leakage through shipping, and is Amazon ISTA 6 compliant.
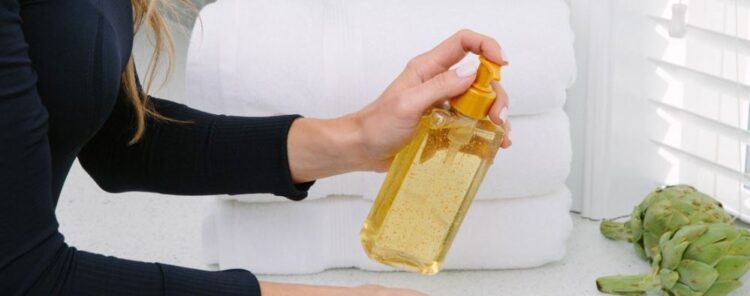
5. Fruits Packaging
New Punnet Easier to Recycle, Uses Less Plastic – Novolex
Novolex has originated a new 100% mono material protective soft-fruit punnet gratitude to its revolutionary MONOAIR cushion technology.
Traditionally, punnet bases have needed an additional layer of bubble padding added with a glue adhesive to defend soft fruit from bruising and spoiling in transit. Still, the padding must be removed from the container to be recycled appropriately.

6. Bio-Based MonoMaterial
a. PUREBARRIER Technology – Ahlstrom-Munksjö’s
They are introducing groundbreaking PureBarrier, an oxygen and gas barrier mono material made of 100% cellulose fibers. PureBarrier is the latest bio-based material to replace plastic or aluminum film in barrier packaging such as paperboard cans and lids.
PureBarrier is a unique technology platform based on Genuine Vegetable Parchment that brings a host of opportunities to pack everyday products more sustainably.
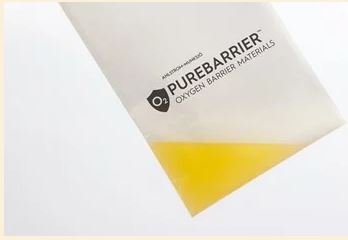
b. Renewable bio-PP product with Borealis – Emballator
Emballator, a foremost producer of packaging solutions, and Borealis, a leading provider of innovative polyolefins clarifications, are expanding their portfolio in close partnership.
Borealis is presenting Emballator with bio-based polypropylene for pails and containers. The raw material is manufactured from used and recovered residue vegetable oil and cooking oils.
“For PE products, it has been possible for many years to produce a product in bio-based material, but for PP, until presently, it has only been possible to create bio-PP based products from renewable sources with the ISCC PLUS certified mass balance principle.

7. Baby Food Packaging
First fully recyclable baby food pouches – GualaPack
Pouch5 is a 100% mono-material doypack choice designed to be easily recycled in the PP stream, certified by self-governing institutes Cyclos-HTP and Interseroh Dienstleistungs GmbH. This indicates that pouches can be collected and turned into new non-food products within a Circular Economy framework after use.

Compliant with both EU and FDA food regulations, Pouch5 is obtainable in two versions: hot-filled and pasteurized shelf-stable products and cold filling/dairy applications. It’s high oxygen and water vapor barrier guarantee product protection equivalent to conventional pouches.
8. Frozen Food Packaging
Tray PET – WALKI
The demand for ready-made meals and frozen food has seen steady growth during the pandemic, as consumers want easily prepared meals and minimally processed food with no additives and long shelf lives. Typically, ready-made meals and frozen food have been served on trays made of plastics and aluminum. Walki is now introducing more sustainable options with its broad portfolio of trays that can be recycled in the paper streams.
Walki®Pack Tray PET is a tray material with a very thin PET-lining that still classifies the material as a monomaterial, making it suitable for recycling in paper streams.

9. Plastic Tubes
a. MonoMaterial Barrier tube – Polyfoil
Polyfoil® Mono-Material Barrier tube (MMB). The Polyfoil® MMB is a high-performance tube, offering superior protection for myriad cosmetics, oral care, and pharma formula. It looks stunning from any shelf with its premium-look finish, even available in metalized design version. The tube body and shoulder are hygienic and pure HDPE with reduced wall thickness, with less than 5% foreign matter. For decoration, we use direct printing (no labels) with inks and lacquers that are EuPIA conform.
It is aluminum-free, chalk-free, and complies with current mechanical recycling demands in the EU and US.
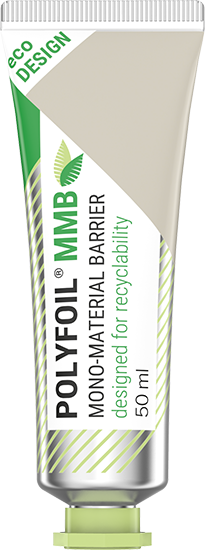
b. Recycling-ready PE tubes – Albea
Albéa produced a new PE cap for a completely monomaterial tube, recycling-ready packaging, a first on the oral care market.
This cap extends to the range of single-material tube solutions given by Albéa, thus taking a different step towards our objective of making 100% recyclable tube packaging by 2025.

Made in Europe, Albéa’s PE Full Diameter Cap is a glossy screw cap compatible with several of our plastic laminate tubes with a diameter of 28mm.
This current PE cap replaces traditional PP caps when merged with PE head and sleeve, and the fully mono-material packaging can be quickly recycled in existing HDPE streams.
ที่มา: https://packagingguruji.com/top-9-advancements-in-monomaterial-plastic/
Sorry, the comment form is closed at this time.