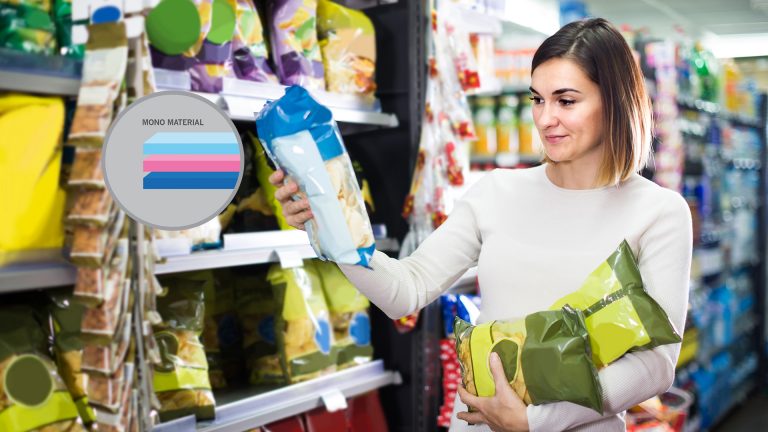
15 May Mono-material Packaging: Packaging for the Circular Economy
Consumers across the world, especially younger generations, have grown increasingly eco-conscious, as reflected in a clear shift in their behavior when choosing products or services. In response, brand owners have to put more thoughts into where their products end up after use. To this end, the principles of the circular economy have been adopted as guidelines for all parties along the supply chain, from manufacturers and brand owners to consumers as well as those involved in the management of post-consumer wastes.
In the plastic industry, packaging makes up the largest portion of plastic usage. Its high demand is thanks to its ability to preserve the quality and prolong the shelf-life of the product inside. Among the many types of plastic packaging is flexible packaging, which is usually made of a film consisting of layers of materials that give the packaging different properties and allow it to serve multiple purposes at the same time. For instance, a flexible packaging can, simultaneously, block oxygen and moisture from getting inside, provide enough strength to protect the product inside, resist to heat, and display sharp and clear prints.
Flexible packaging generally consists of multiple layers, whose functions can be classified into three major categories. For each of these, manufacturers choose materials that have suitable properties.
The outermost layer is for printing labels, logos, or other details that communicate a message to consumers and is generally made of films with high stiffness and low elongation, providing sharp and clear prints. The popular materials for this layer are PET, nylon, and BOPP (biaxially-oriented polypropylene).
The middle layers act as barriers against oxygen and moisture, which are major agents that damage or degrade products in powder form, such as coffee powder and non-dairy creamer, which can easily clump up when exposed to oxygen or moisture. Therefore, these layers need to be made from materials with low oxygen transmission rates (OTR) and water vapor transmission rates (WVTR), such as aluminum foil or metalized films, which are filmed coated with vaporized aluminum.
The innermost layer is called a sealant because its function is to create a perfect seal and prevent leakage. Moreover, it provides strength to the overall packaging, so it has to have good toughness. Some materials can seal through food particles or oil droplets that splash up the sides of the packaging while the product is being packed. Generally, the sealant layer is made of materials with low melting points, such as LLDPE (linear low-density polyethylene) and CPP (cast polypropylene), so that it can be sealed quickly at low heat, thus, increase the productivity.
As flexible packaging consists of inseparable layers of different materials with different properties and melting points, it does not lend itself to recycling; to achieve maximum efficiency, the material has to be homogeneous. When a flexible packaging is recycled as it is, the recycled plastic will be inferior in quality because the melting points of the materials of the three layers usually differ vastly. For instance, a packaging for snacks or coffee usually consists of layers of PET, aluminum, and CPP. When it is melted at a low temperature, the aluminum layer, which has a high melting point, will not melt, and will contaminate in the recycled material. In contrast, if the packaging is melted at a high temperature, the CPP layer, which has a low melting point, will be degraded, destroying its useful properties.
As the market is increasingly seeking to achieve the circular economy by recycling plastic packaging at maximum efficiency, packaging manufacturers are looking for substitute materials, and this is where mono-material packaging comes in.
The key characteristic of mono-material packaging is the use of films that are made entirely out of a single material, such as all PE or all PP in each layer. To achieve the properties of the existing packaging, the challenge for plastic resin manufacturers is to produce the better resin than the existing one with the help from technology and innovation or the use of additives to ensure that their products can replace the materials mentioned above.
Mono-material is an emerging trend in recyclable packaging, and plastic resin producers across the world are pouring their efforts into developing innovative solutions. In response, Chemicals Business, SCG is also developing PP-based and PE-based mono-material solutions to serve all major packaging applications.
As brand owners and manufacturers are reinventing themselves and playing an active role in realizing the circular economy, we, the consumers, will have to not only play our part as responsible consumers, but also change our behavior, starting with simple things such as fully utilize the resources, correctly sort the waste, and properly dispose them. With these simple changes, we can ensure that useful resources can be recovered and recycled whereas non-recyclable materials can be sorted out and handled properly.
ที่มา: https://www.allaroundplastics.com/en/article/innovation-en/3073/
Sorry, the comment form is closed at this time.